Common Problems and Solutions of Tundish Refractory Configuration
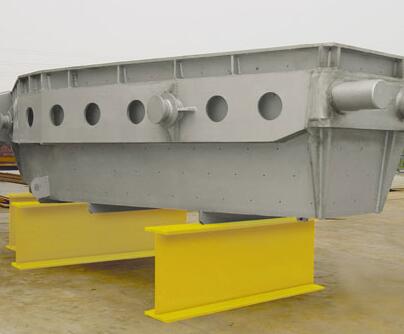
Common problems in the use of tundish refractory materials, some of which are quality problems of the materials themselves, and some of which are related to site construction, require careful observation and analysis. So follow me and find out the problems and solutions of tundish refractory configuration.
Low Strength Dry Material
After vibration and baking, the dry material will often have no strength or low strength, which will easily lead to bag collapse and affect the case production of continuous casting. After long term observation and analysis, it is concluded that the main reasons for the non strength or of dry materials are as follows:
(1) baking problems: the tundish roasting device used in the steel plant is a gas roaster, which will cause a lot of tar in the pipeline or damage to the burner after long-term use, resulting in poor local baking effect and no or low intensity.
(2) dry material damp ingress: dry material is composed of 70% particles and 30% fine powder. Fine powder contains magnesia sand and binding agent. Due to the high specific surface area, fine powder easily absorbs water and gets wet.
Solution: First of all, it is necessary to ensure the baking effect of the roaster, regularly purge the gas pipeline, remove tar and dust, and timely replace damaged burners; second, it is necessary to ensure that dry materials dry and mix evenly.
Turbulence Floats
Sometimes, the turbulizer will go through hell on the surface of the liquid steel in the process of multi furnace continuous casting, which can not stabilize the flow of steel and protect the impact zone, which is adverse to the quality and safety of the liquid steel.
Solution: Adjust the formula of turbulizer and control the expansion under high temperature.
Water Hole Cracking and Infiltrating Steel
The cracking of zirconium core in the pouring process leads to the seepage of steel, which often forces the continuous casting to block the production or shut down. The analysis shows that the main reason for the fracture is the poor thermal shock resistance of the zirconium core.
Solution: Volume density of zirconium core can not too high, and the higher volume density, worse thermal shock resistance.
Large Casing Rupture
Large casing is located between the water inlet of the ladle and the tundish, and its metallurgical function is to prevent the liquid steel from splashing and being oxidized during the flow of liquid steel from the ladle into the tundish. The most common problem in the operation of large package casing is fracture over rupture.
Solution: First, use materials with small thermal expansion coefficient and elastic mold to produce the casing to improve the thermal shock resistance. Second, when the casing and the water outlet are unable to share, external force cannot be applied to the lower part of the casing.